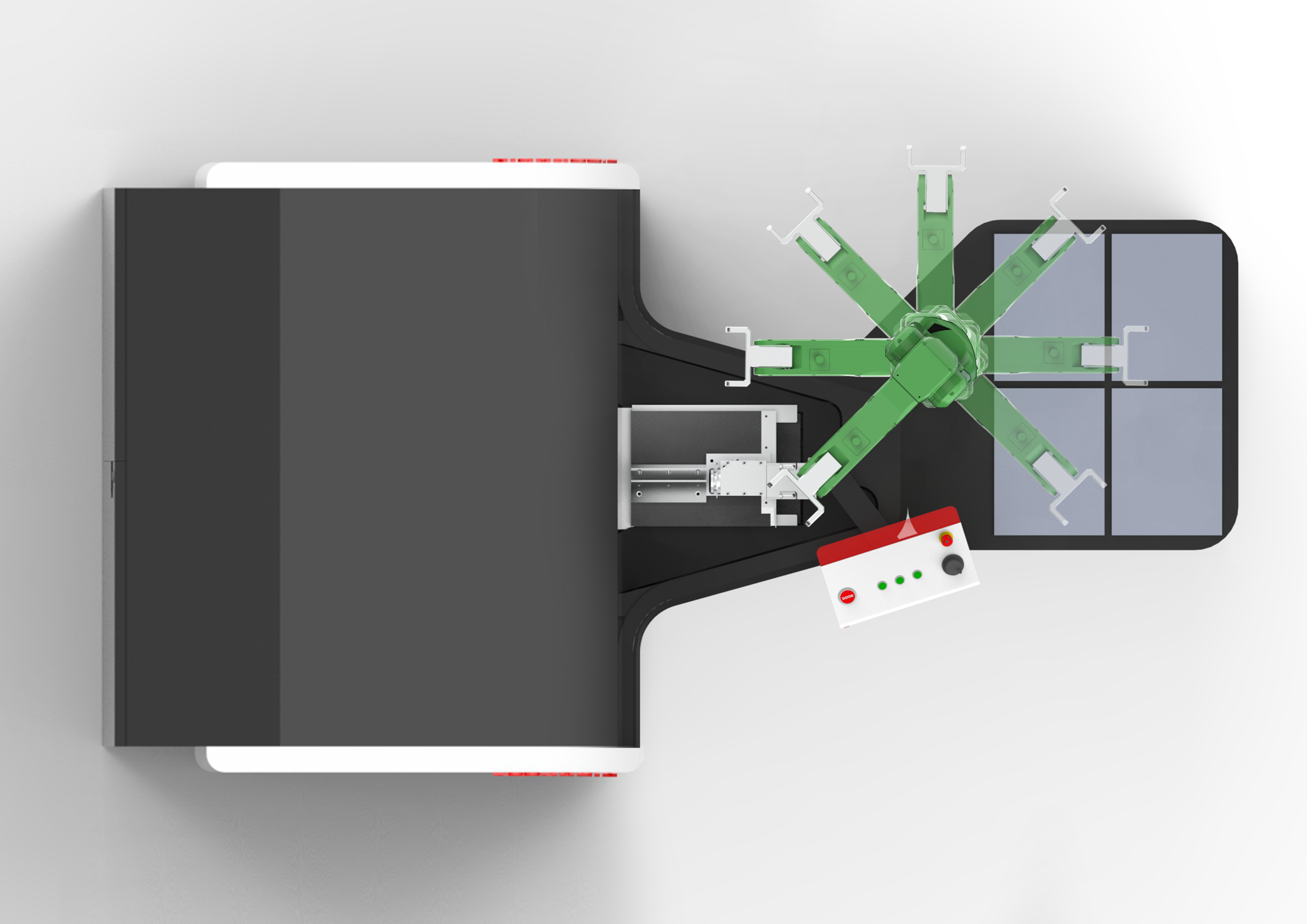
The perfect interplay between the centreless CUBE 350 external cylindrical grinder and a robot results in productivity gains when producing small batches.
TSCHUDIN AG introduces its compact CUBE 350 centre less external cylindrical grinder with a collaborative robot for the first time. The high-precision, three-axis CNC grinder forms a perfect symbiosis with the robot, allowing for small batch production to be automated and enabling further increases in the CUBE 350’s productivity.
The automation solutions used in the CUBE 350 enable users to achieve significant productivity gains. The machines particularly quick and flexible changeover times help to minimise machine downtime. During the development of the CUBE 350, the engineers at TSCHUDIN dedicated themselves to improving the device’s user-friendliness and ease of use.
Minimal installation area
What sets the CUBE 350 apart in particular is its very small installation area (2558 x 1735 x 1320 mm). Users only need access to the rear of the machine to perform maintenance and servicing tasks, which means that several machines can be positioned together without any gaps. The philosophy when developing the CUBE 350 was to have “minimal area and maximum efficiency”.
The grinder can be manually loaded in a safe and ergonomic way both by right-handed and left-handed users – a feature for which a patent application has been filed. The machine has a unique design with digitalised set-up and grinding processes to ensure the highest possible process stability and machine availability. Linear drives on the X, U and W axes ensure flexibility and productivity. The CUBE 350 was specifically developed for machining small components with part diameters of up to 20mm.
Low-maintenance machine design
The CUBE 350’s simple and low-maintenance machine design helps to reduce operating costs. The natural granite machine frame and carriages guarantee thermostable, high-precision and a safe grinding processes. One major benefit of the machine is that it allows for easy and CE-compliant loading and unloading outside the grinding zone. TSCHUDIN’s “easy” software, which the company developed in-house, makes the device easy to operate and automate.
A wide range of process options
The patented, movable workpiece support ensures that the following range of process options is available: Roughing and finishing in a dual cycle, grinding sharp edges and controlled dressing of taper and radius. Its areas of application include plunge-cut grinding, grinding several operations in a single cycle, oscillation of the component during grinding and throughfeed grinding. This versatility means that the CUBE 350 is suitable for a wide range of applications – from toolmaking for very small batch sizes to medical technology and mass production in the automotive industry. Various materials can be processed – from steel to aluminium, glass, titanium, carbon, ceramics, germanium and silicon, amongst many others.
In addition to the CUBE 350, TSCHUDIN also offers the ecoLine and proLine series. The patented three-axes concept of the ecoLine 400 and 600 simplifies the overall system and ensures reliability and the best machine availability. The proLine (400 and 600) also features the patented fourth CNC axis for moving the regulating wheel vertically. The regulating wheel’s support and dressing tool are positioned securely, level with the grinding wheel. It is not necessary to adjust the height of the support, which means that the grinding geometry remains constant during the entire grinding process.
Paving the way for innovation
TSCHUDIN AG is on course for growth. In addition to establishing a new subsidiary in China, the Swiss company is also looking to increase its market share in Europe. In May 2019, a new industrial building with a five-storey office annex was opened at the TSCHUDIN headquarters in Grenchen, Switzerland. The high-tech company is fully focussed on the fields of research and innovation. The company says that it sells tailor-made solutions, not just machines. TSCHUDIN is looking to enlarge its team. A niche technology like centreless grinding provides young, creative engineers with boundless possibilities.